Against the backdrop of the global energy transition, biomass pellets have become an increasingly favored choice by both market and policy as a clean, renewable energy source. This article focuses on the trial wood pellet production line, explaining how a biomass pellet factory can use small-scale trial production to verify processes, evaluate market demand, and plan capacity to achieve high cost-effectiveness. We also discuss energy-saving and environmental requirements and ABC Machinery’s technical advantages, helping businesses reduce risks and speed up return on investment.
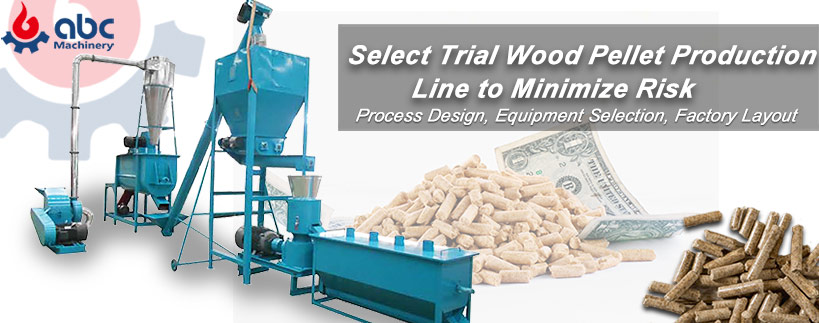
Choose Best Trial Wood Pellet Production Line
Why configure a Wood Pellet Pilot Production Line?
A trial production pellet line refers to a small-scale wood pellet production line built before full-scale production, designed to test the adaptability of raw materials such as sawdust, rice husks, and straw, as well as the stability of the production process. It not only validates the design of the wood pellet plant and the selection of pellet machinery, but also ensures the feasibility and stability of the biomass wood pellet manufacturing process. Through trial production, you can:
≥95% molding rate process verification
-
Under real continuous production conditions, test ≥6 raw materials (pine, birch, poplar, coconut shell powder, rice husk, corn stalk) for pellet density (≥1.1 g/cm³), moisture content (8–12%), and calorific value (≥4,600 kcal/kg), ensuring scientific and reliable process solutions.
Reduce biomass pellet factory investment risk by 20–30%:
-
Discover bottlenecks such as material blockage, abnormal wear of ring die and rollers, and high energy consumption in advance.
-
Compared to directly building a large pellet line that could cause millions of dollars in losses, trial production lines can complete parameter optimization within 2–3 months and avoid expensive later modifications.
Quickly establish standardized production systems:
-
Based on trial production data, develop SOPs (standard operating procedures), QC standards, and maintenance schedules to achieve a one-time compliance rate ≥98% for subsequent mass production.
Flexibly support market testing:
-
In 1–2 weeks, the wood pellet machine can switch die hole diameters (6–10 mm) and adjust compression ratios, producing small batches of wood pellets for customer testing, including calorific value, mechanical durability (≥97.5%), and ash content (≤1.5%), accurately matching diverse markets.
Wood Pellet Manufacturing Equipment in Production Line
Because a trial wood pellet production line involves complex factors such as raw material characteristics, pellet manufacturing process parameters, and market strategies, this article cannot cover all details. Feel free to contact ABC Machinery for free professional and customized consulting.
How to build a more cost-effective wood pellet production line
Directly investing in a large, fully automated biomass pellet plant often requires millions of dollars, with a payback period of 3–5 years. In contrast, starting with an initial capacity of 0.5–1 ton/hour small-scale trial production line can reduce upfront investment by 40–60% and shorten ROI to 12–18 months, significantly improving capital efficiency. Here are four data-driven planning strategies to help businesses achieve the best return on investment:
Optimize cost structure and control total cost of ownership (TCO)
-
Initial wood pellet manufacturing equipment cover crusher, dryer, pellet mill, cooler, screener, and automatic packaging system.
-
Operating and maintenance costs (OPEX) average about 12%-15% of the investment annually, with electricity accounting for 60%, fuel 25%, and labor/other 15%.
-
Modular design and wood pellet making machine upgrades can save 20%-30% in new construction and installation costs.
-
Depreciation period planned for 5–7 years, with key wearing parts (ring die, roller) averaging 3,000–5,000 hours lifespan; regular maintenance extends the life of the pellet press machine by 20%.
-
Relying on self-produced core parts, ABC Machinery keeps ring die and roller costs ~15% below the industry average, and offers complete lifecycle maintenance plans, helping biomass pellet factories reduce overall O&M costs by 10%.
Capacity and process design support flexible expansion
-
Initial pellet production line capacity recommended at 0.5–1 t/h, with a trial period of 3–6 months to mature the production process.
-
Equipment power configuration reserves 30%-50% redundancy, supporting future upgrades to 3–5 t/h.
-
Die hole diameter adjustable from 6–12 mm, meeting different raw materials and market needs.
-
ABC Machinery’s patented technologies support fast module assembly and expansion, shortening upgrade time to 1–2 weeks, far less than the industry average of 4–6 weeks.
Energy saving and environmental compliance
-
Intelligent control systems reduce energy consumption of biomass pellet making machine by 10%–15% compared to traditional processes.
-
Dust emissions controlled to ≤30 mg/Nm³, meeting EU and US standards.
-
Final pellet moisture controlled at 8%–12%, ash content below 1.5%, suitable for premium export markets.
-
High-efficiency dust and exhaust recovery systems purify emissions to achieve near-zero discharge.
-
ABC Machinery develops ISO 50001 energy management compliant solutions, helping pellet factories pass green plant certification, reduce environmental compliance risk, and enhance CSR image.
Wood Feed Pellet Making Process Flow Chart
Why choose ABC Machinery?
As a professional wood pellet equipment supplier, ABC Machinery offers rich R&D experience and a solid customer reputation. Choosing us means you’ll enjoy:
-
Shorter commissioning cycle by 30%: Only 2–3 months on average to reach stable mass production, compared to the industry average of 4–6 months.
-
Wider raw material adaptability: Compatible with ≥8 wood, straw, coconut shell powder, etc.; capacity variation within ±5% on the same wood pellet machine line.
-
Annual electricity savings of 10–15%: Proprietary ring die plus intelligent variable frequency control.
-
Downtime reduced by 20%: Independent quick-disassembly design, ring die replacement averaging 1.5–2 hours vs. 3–4 hours industry average.
-
ROI analysis & process simulation: Digital capacity simulation report and financial payback model before building the line, supporting loan/government subsidy applications.
Trial Wood Pellet Production Line for Sale
In today’s competitive biomass energy market, the trial wood pellet production line plays an irreplaceable role connecting R&D and mass production. It helps verify process feasibility, control risks, speed up innovation, and adapt to markets—significantly boosting ROI. Choosing a high-performance, flexible trial line and a trusted partner is the only way for enterprises to achieve green transformation and sustainable growth. Contact us to get free and professional answers immediately.