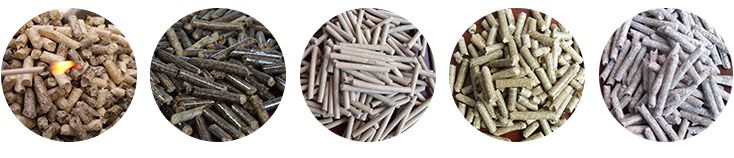
Wood Pellets Made from Different Biomass Materials
Offer customzied wood pellets manufacturing system from wood wastes (sawdust, branches, forest cleaning deadwood and leaves, small trunks or crop wastes, etc) to wood pellets or briquettes. (Related Project: 3ton/h Wood Pellets Production in Malaysia)
Wood pellet plant is constructed to process biomass materials such straws, grass, peanuts, shells, wood squanders, for example, branches, sawdust, shavings, and whatever other ignitable materials accessible into biofuel pellets for the heating, warming, cooking and different purposes. (Read more about wood pellets factory setup cost >>)
Increase Production of Wood Pellets Manfuacturing Plant
Industrial Sawdust Pellet Plant
Vertical Pellet Making Machine
Common Wood Pellet Processing Flow: Wood Chipping, Crushing, Pelletizing, Pellets Cooling, Pellets Bagging.
Raw materials and operating factors are what relate to the capacity of wood pellet machine. Consequently, the quality of the raw materials is a great deal directly determines the pelletizing efficiency. Also, the determining factors are also vital to the production capacity of the pellet mill. The big question, however, is how to keep the best of the pellet mills. (Related Post: Cost of Producing Wood Pellets)
If you are about to establish your own wood pellets factory and become one of the wood pellet fuel manufacturers, here are some suggestions to increase the production output. You can take our 5ton/h wood pellet processing equipment for reference.
Requirements for Raw Materials to Be Pelletized
The following measures can apply to raw materials:
- The raw material size of the pellet mill is required to be readily produced in high-grade pellet status hence ensure you give essential attention and concern to the raw material size.
- Secondly, ensure the cleanliness of the raw materials. There is a fact in the statement, the cleaner the raw material then definitely the high the effectiveness of the pellet mill machine.
- Moisture is another key feature to ensure your raw material has. Ensure that then your raw material is not too moist or less. Too much humidity can alter the pellet quality and result in more energy consumption and importantly wear out of equipment. Ensure then that the moisture is between 8-15 %.
- Hardness is another issue to consider for your raw materials. Ensure that they are not too hard to ensure easy making process of the pellets and also avoid damaging the spare parts.
- Further, ensure that your wood/biomass pellet mill raw materials are highly viscous so as they can easily adhere to the inside part of the pellet mill. Failure this, then the production capacity will be reduced while also altering the normal operation of pellet mill. Lastly, on the raw material, the density should be high to ensure that they a more significant capacity of the pellet mill.
You maybe also interested in: How to make pellets from straw? How to make pellets from coco coir? Or how to make corn stalk pellets? Any other questions about starting wood pellet business plan, don't hesitate to contact us!
Tips for Wood Pellets Manfuacturing Equipment Operation
Operating factors ought to have the following features to ensure the best of the commercial wood pellet manufacturing equipment. (HOT Sale Product: Portable Pellet Mill >> )
- What adjustment of the roller and ring die to appropriate location is vital. Correct pressure is a guarantee to good outcomes for the pellet density.
- Secondly, ensure that you replace the old ring on the die on time always since it is a wearing out part together with the roller. If you observer uses them, then the pellet machine will not perform adequately as required.
- Ensure that you have selected the appropriate ring die specification. This is to provide that you keep good and quality pellets.
- Again ensure that uniform raw materials are feeding the wood pellet making machine to maintain the required friction factor among raw materials, rollers and the ring die that is on the inside.
- Adopting of a cooling system is also an essential operational factor. This prevents the pellets from loosening. After cooling the proper temperature should be +3-5 higher than the average room temperature.
Click here to know more about empty fruit bunch pellet mill >>
The most fundamental step of the operational factor is the strict use of the practical manual. Consequently, well maintained and cleaning of the equipment if necessary. Lastly, and to emphasize, a uniformed raw material will ensure proper coordination of operational factor for the pellet mill efficient functioning and durability.