How to choose, use and maintain ring die pellets presses?
Ring Die Pellet Press for Sale
Model | Capacity (kg/h) | Power (kw) | Dimension (mm) | Weight (kg) |
BPM35 Pellet Mill | 500-800kg/h | 30*2+0.75+0.75kw | 2150*1950*1900mm | 2200kg |
Buy Pellet Mills with High Quality Ring Die
Firstly, pay attention to the material of the ring die. The common materials of ring die are stainless steel and carbon steel. The production process includes forging, cutting, drilling, heating and so on. Both the material and the production process affect the ring die’s quality, service life and the pellet press capacity.
If you know little about the technology, then the simple way is to buy from large and reliable factory or manufacturer. If you just pick a small factory for cheaper price, you will suffer from ring die blockage, die holes burst, poor quality of final pellets and many other problems in the process of using. For most small factories, the drilling process of ring die is manually with simple equipment. The ring die quality all relies on the attitude and skill level of the worker. Some holes are crooked which can cause discharging and blocking problem. Beside, due to the equipment and technology limitation, the quality of polishing also cannot up to the standards in small factories.
Pay Attention to the Thickness of Ring Die
The thickness of ring die is another key factor for the pelleting output and quality. Ensure that it is designed appropriately. Talking about the thickness, you should know about the ring die compression ratio (equal to length of die hole/ diameter of hole). Higher compression ratio means pellets with higher density and smoother surface. However, if the compression ratio is set too high, the pellets discharge will become difficult, or even block the pellet press machine. But the question is how to tell if the compression ratio is appropriate? In fact, it is not a simple question. The compression ratio is affected by many factors including die hole diameter, final pellets length and pelletizing materials.
Make High Quality Biomass Pellets
Make Sure the Press Roller Works Well with the Ring Die
The clearance between the press roller and pellet die should be appropriate too. Generally, it is between 01.mm and 0.3mm. If too large, the extrusion force will be inadequate which can cause pellets discharging difficulty and end to block of pellet machine. If too small, the press roller and pellets die will likely to be damaged. It is a difficult task to adjust the clearance. Experience and skill is required.
Basic Ring Die Maintenance Of Ring Die Pellet Mill
During use, you would face with ring die blockages, abrasive wear inevitably. These problems should be solved timely, or else, the pelletizing production is bound to be lowered. The power consumption will increase too, and the pellet mill might even be damaged. To avoid these terrible accidents, we should do routine inspection maintenance timely and seriously. Below is what you can do:
- Find the blocked holes in the ring die and drill through the holes.
- Polish the irregularities surface made by the hard impurities in the raw pelleting materials such as iron scraps.
- Repair the shrinkage cavity by enlarge these holes. The angle of taper mouth should be 60°.
- When stop running the ring die pellets press for a long time, stuff the ring die holes with oily materials to keep good performance for the next use.
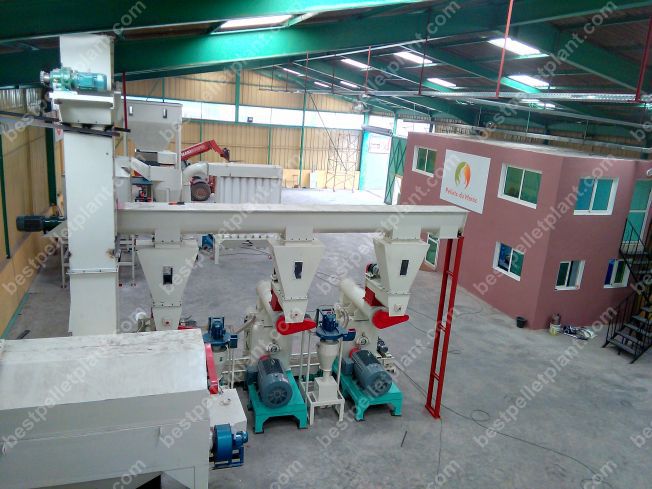