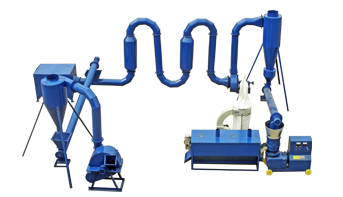
For the ones who plan to build a small pelletizing unit with capacity between 500kg/h to 800kg/h, or want to start a small pellet making factory with limited budget, this automatic mini pellet plant is definitely what you need!
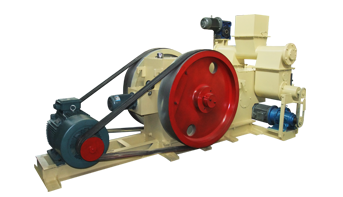
Mechanical stamping briquette plant can make both large biomass briquettes and small fuel pellets.
Processing Various Biomass Materials
Long Service Life, Good Strength
High Production Efficiency
How To Build A Wood Pellet Production Line?
In recent years, the popularity of wood pellets is increased tremendously. Due to its convenient and economic, more and more people choose pellet fuel for heating and cooking, including individual and commercial application. So the demand for wood pellets is growing rapidly. Now, invest in wood pellet production is promising and profitable in a long run. The development of bio-fuel is good to our environment and agricultural industry. To promote the development of bio-fuel, many countries have regulated the related policy and taxed, including China. Actually, wood pellet plant can process more than just wood materials. Almost all kinds of biomass materials can be used as feedstock for making pellets.In this article, let’s take a further look at wood pellet line and the details of pellets manufacturing process.
Characteristic of Biomass Pellet Fuel
Biomass Pellet Fuel Make From Different Materials
Almost all kinds of biomass substance can be used to make biomass pellets including bamboo, palm fiber, bagasse, corn cobs, maize stalks, cotton stalks, wheat straw, rick husk, twigs, tree branches, bark, wood shavings, sawdust and so on. Compared with raw feedstock, biomass pellets have the properties of ecological and sustainable, higher energy dense and are easier and cleaner to use. All these advantages make biomass pellet fuel attractive and hot sale.
Build Your Own Wood Pellet Plant
Pre-treatment
Small Scale Pellet Plant
Large Scale Pellet Plant
How to Manufacture Biomass Pellets?
The key parts of pellet machine is pellet die and pellet roller. During the pelletizing process, high pressure and high temperature will generated between the die and roller. The biomass feedstock will fuses together under the high temperature and then be extruded through the holes in the pellet die, forming a cylindrical solid mass. Below is the process of complete biomass pellet plant.
Various Kinds of Biomass Materials Suitable for Making Bio-fuel Pellets
-
Raw Material Grinding
-
Drying
-
Pelletizing / Extrusion
Although various kinds of biomass materials are suitable for making pellet fuel, some of them are better than others for pelletzing. Sawdust is most common and best materials, because of contenting lignin. Grass is also good choice, but grass pellets are less dense than sawdust biomass pellets. For the biomass materials which are hard to process, mix with some sawdust or add appropriate binder to help.
-
Cooling
-
Packaging